(1) Selection of heat-resistant rubber type In order to reduce or eliminate the vulcanization reversion phenomenon of vulcanized rubber, a rubber with a low double bond content should be selected. Various rubbers have different thermal stability and different extreme vulcanization temperatures. Suitable for high temperature and rapid vulcanization are EPDM, IIR, NBR, SBR and so on.
(2) Adopting an effective or semi-effective vulcanization system Because CV vulcanization system has a high content of polysulfide cross-linking bonds, it is easy to produce vulcanization and reversion at high temperatures, so CV is not suitable for high-temperature rapid vulcanization systems. The high-temperature fast vulcanization system uses an effective EV with a high content of monosulfur and disulfide bonds and a semi-effective SEV vulcanization system, and the vulcanized rubber has good heat-resistant oxygen aging performance.
Generally, a high-promoting low-sulfur and sulfur-supported vulcanization compound is used, and the latter is preferably DTDM, and has a wide range of scorch time and vulcanization characteristics, and is easy to meet rubber manufacturing requirements. TMTD is limited in application due to short scorch time and severe frosting. Although EV and SEV have better effects on high-temperature vulcanization than CV, they are still not ideal enough to completely solve the disadvantages of vulcanization reversion and poor flexural resistance caused by high-temperature vulcanization. A better method should be found.
(3) Special compounding of vulcanization In order to maintain the crosslink density of the vulcanizate at a high temperature, a method of increasing the amount of sulfur, increasing the amount of the accelerator, or both may be employed. However, increasing the amount of sulfur will reduce the vulcanization efficiency and increase the content of polysulfide crosslinks; while increasing the sulfur and accelerator, the vulcanization efficiency will remain unchanged; while maintaining the amount of sulfur and increasing the amount of accelerator, it can be improved. Vulcanization efficiency, this method is better and has been widely promoted and applied in the tire industry.
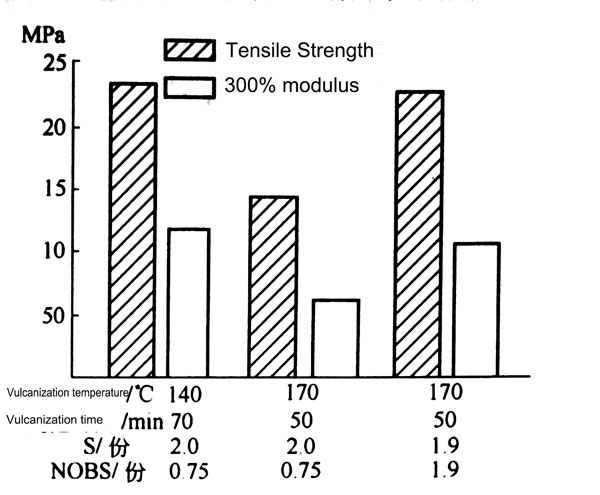
Under the condition of keeping the amount of sulfur constant and increasing the amount of accelerator, the crosslinking density and the tensile strength retention rate. If DTDM is used instead of sulfur, the effect is better, and under high-temperature vulcanization conditions, excellent performance like CV vulcanizate can be obtained.
Synthetic rubber vulcanization system is less sensitive to temperature than NR, so the combination of NR and synthetic rubber is particularly important, and the system after use not only maintains the stability of crosslink density at high temperature vulcanization, but also maintains the best vulcanizate. Physical properties are an effective method for rubber products to be vulcanized at a temperature, shortening the curing time, and improving production efficiency.